Im Mittelpunkt steht für Entwicklungsleiter Harald Sima der Anspruch, Technik für die Menschen zu entwickeln: „Das macht unsere Arbeit so spannend, aber auch so schwierig.“ Sicherheit steht für den promovierten Maschinenbauer dabei an erster Stelle: „Eine Prothese muss verlässlich sein und sich immer gleich verhalten.“ Daher ist der hausinternen Entwicklung auch eine 99,9-prozentige Verlässlichkeit nicht gut genug. „Das würde ja bedeuten, dass Prothesenträger:innen bei jedem 1000. Schritt hinfallen – wir brauchen eine noch höhere Zuverlässigkeit.“
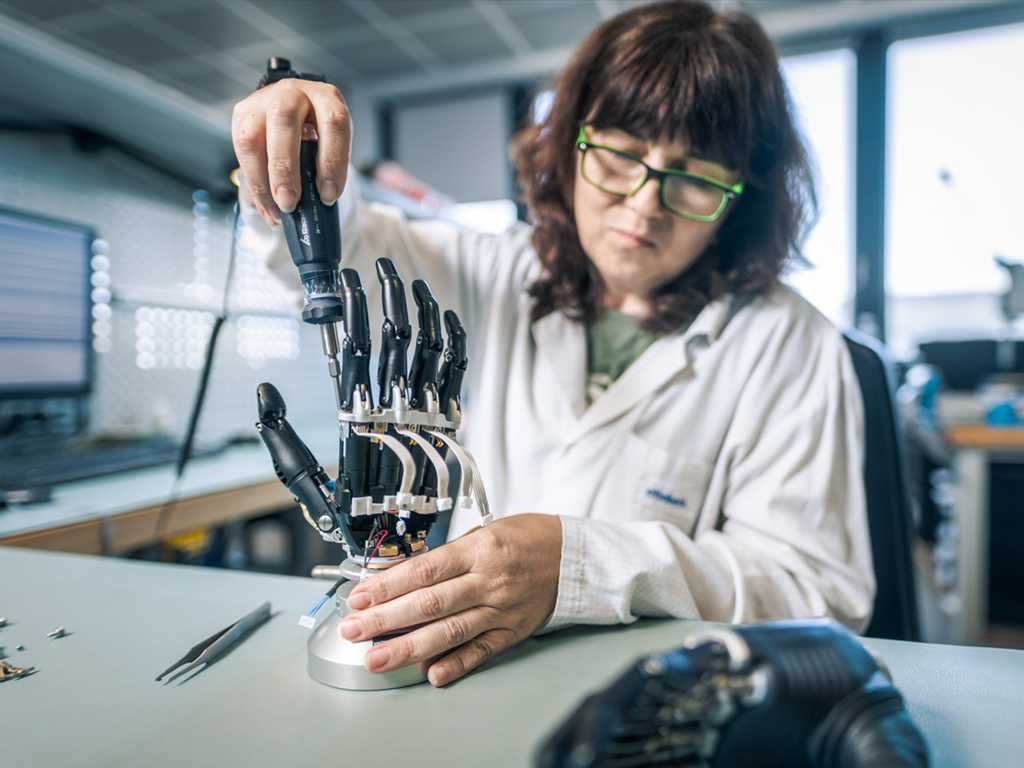
Von den insgesamt 650 Beschäftigten arbeitet jeweils rund ein Drittel in den Bereichen Entwicklung, Fertigung und anderen Bereichen wie Controlling, Humanressourcen und Marketing. Der Rundgang durch die Abteilungen beeindruckt durch eine Vielfalt an Maschinen und Fertigungsbereichen. Einmal flimmern biometrische Belastungsmodelle über den Schirm, andernorts spritzen Mitarbeiter:innen Kunststoffteile, die „wir in ihrer Exaktheit und geringen Stückzahl selbst am besten fertigen können“. In Werkstätten werden die mechanischen Teile von Arm- oder Beinprothesen gedreht, gefräst, verschraubt und gelötet. Auch das Bestücken von Platinen, die elektronischen Steuereinheiten der Prothesen, findet statt. Hier arbeiten Fachkräfte und Lehrlinge aus den Bereichen Mechatronik, Software und Biomechanik, aber auch Leute, die bei Simulationen und Algorithmen sattelfest sind.
Hart im Nehmen
In den Werkstätten regiert die Technik. Nach der Endmontage wird jede Prothese nochmals akribisch auf ihre Funktionsfähigkeit und Haltbarkeit hin geprüft. Für Sima ein wichtiger Schritt, denn „die Produkte müssen alles mitmachen, was ihre Anwender:innen so tun, und sind neben mechanischen Belastungen auch Hitze, Schmutz, Feuchtigkeit und Reinigungsmitteln ausgesetzt“. Zur Prüfung von Material und Form der Prothesen wird eine Vielfalt von Gerätschaften eingesetzt. So werden beispielsweise in einem Gangsimulator Statik und Belastbarkeit der künstlichen Gelenke geprüft.
Arbeiter:innenbetriebsrat Christian Cypra erklärt den aufwendigen Check am Beispiel eines C-Leg-Kniegelenkes: „Das Kniegelenk wird programmiert, die Anschläge werden eingestellt, damit die Sensoren zielgerichtet arbeiten und alles den Anforderungen entspricht.“ Nach diesen notwendigen Durchläufen kommt das C-Leg auf den Gangsimulator und muss 500 Schritte bestehen: „Am Ende wird ein manueller Ausgangstest durchgeführt, bei dem alle Funktionen des Kniegelenks geprüft werden. Wenn alles positiv abgeschlossen wird, ist das C-Leg bereit zur Auslieferung.“
Lernfähige Prothesen durch KI
Auf den Digitalisierungszug ist Ottobock längst aufgesprungen, die Myo-Technologie nutzt die Vorteile von KI: „Die Prothese lernt von den Anwender:innen, dadurch ergibt sich eine nie dagewesene Induktivität, also Leitfähigkeit der Steuerung.“
Welche Vorzüge eine myoelektrischen Prothese hat, veranschaulicht Elektrotechniker Patrick Mayrhofer. Der junge Entwickler, selbst Träger einer Handprothese, demonstriert die Unterschiede zwischen einer konventionellen Versorgung und dem Myo-Plus-Mustererkennungssystem mit acht Elektroden. Die Steuerungspunkte liegen am Muskel des Armstumpfes auf und helfen dabei, die Greifbewegungen der Prothese möglichst intuitiv zu erreichen: „Menschen wie ich, die einmal eine Hand besessen haben, können die Bewegungen der Hand visualisieren und dadurch jene Muskeln anspannen, die gebraucht werden, um den gewünschten Griff der künstlichen Hand durchzuführen.“
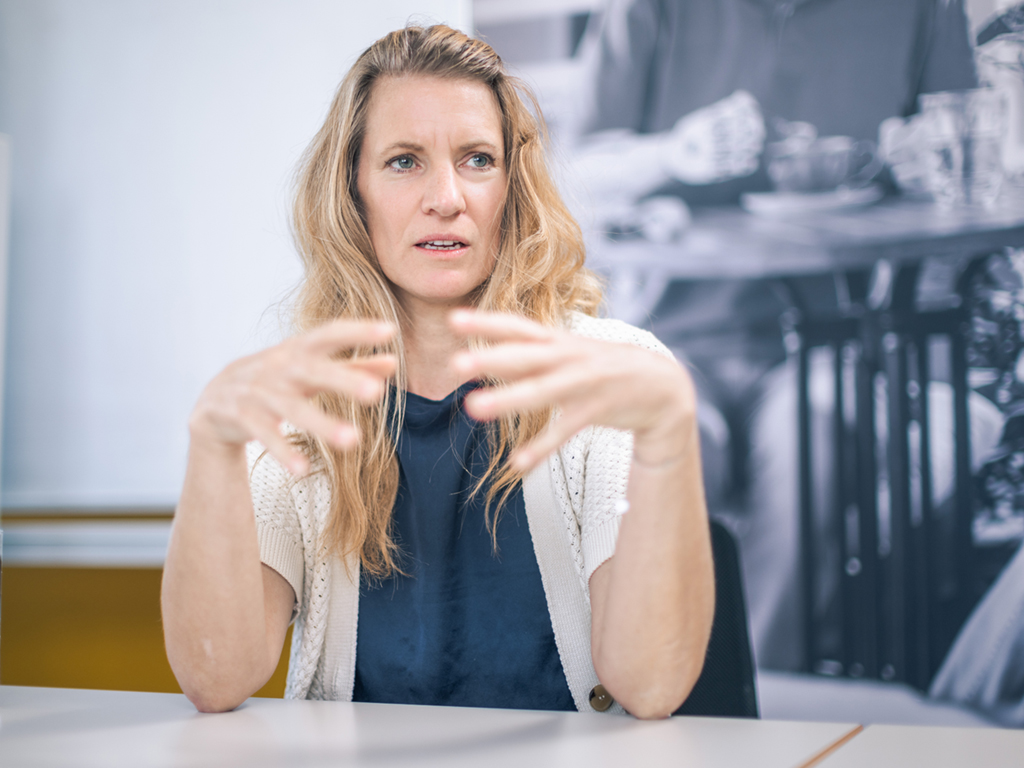
So lernt die Prothese die individuellen Bewegungs- und Steuerungsmuster der Anwender:innen kennen und trainiert sich auf diese Signale. Die KI wertet die gewonnenen Daten aus. Für die künstlichen Gliedmaßen werden neben rostfreiem Stahl Hightech-Werkstoffe wie Carbon, Titan und hochfeste Aluminiumlegierungen verwendet.
An der Schnittstelle zwischen Technik und Orthopädie
Cypra ist sichtlich stolz auf die Breite der Produkte, an deren Herstellung und Prüfung rund 140 Arbeiter:innen beteiligt sind: „Jede Prothesenversorgung ist maßgeschneidert. Wir stellen wie in einem Lego-Baukastensystem einzelne Komponenten für die Orthopädietechniker:innen her. Die exakte Ausgestaltung ist von den Anwender:innen ebenso abhängig wie von ihrer beruflichen Tätigkeit und der Art des Unfalls.“
Die Versorgung der Anwender:innen passiert im Zusammenspiel von Orthopädietechniker:in mit den zuweisenden Spitälern oder Rehabilitationseinrichtungen. Sima erklärt, dass so „unsere Passteile zusammengefügt werden, um eine optimale Versorgung zu erzielen: Wie die Sonderanfertigung aussieht, hängt auch immer von den Bedürfnissen der Anwender:innen ab und davon, wer welche Kosten trägt bzw. was mit der Gesundheitskasse abgerechnet werden kann.“
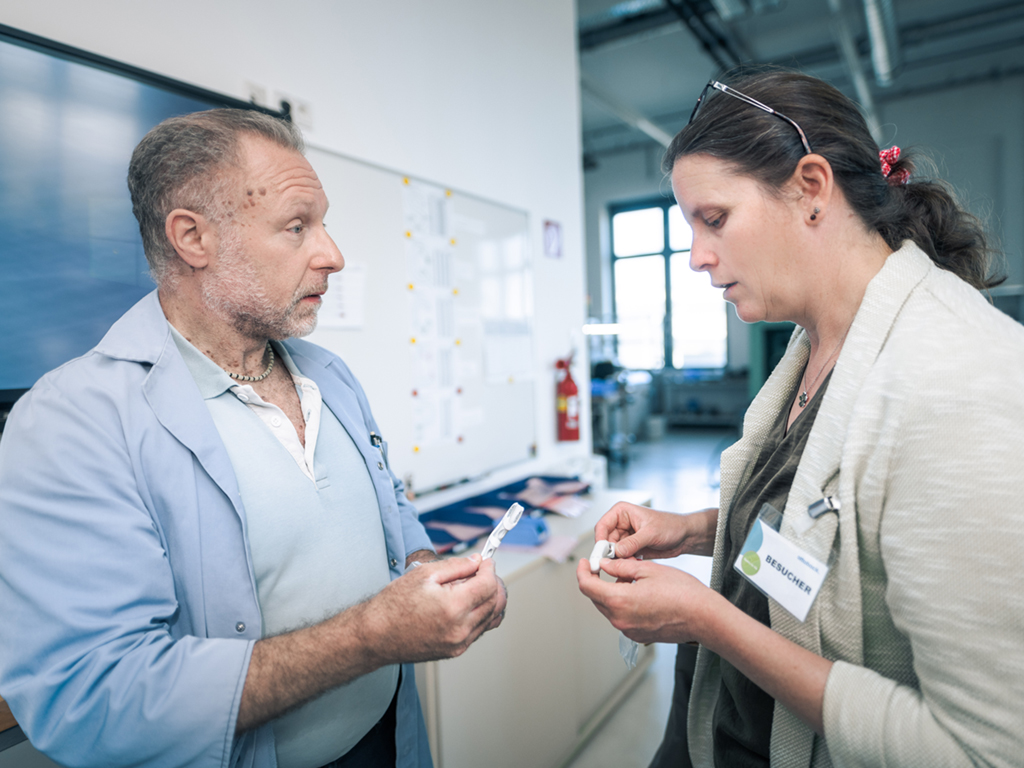
Entwicklerin Birgit Bischof, ausgebildete Physiotherapeutin, arbeitet an der Schnittstelle zwischen Technik und Orthopädie. Sie kennt die Anwendungsmöglichkeiten der technischen Komponenten und weiß, wie die Überleitung zu den Anwender:innen erfolgen soll, um möglichst erfolgreich zu sein. Bischof unterstützt bei Bedarf komplexe Versorgungen: „Zunächst geht es um den Körper und auch darum herauszufinden, welches Potenzial die Patient:innen haben, sich bestimmte Bewegungen mental vorzustellen.“ Reines Handwerk greife hier zu kurz: Auch eine optimale Prothese kann nicht gut genutzt werden, wenn ich nicht gelernt habe, wie ich damit umgehe.“
Individuelles Einzelstück
Orthopädietechniker:innen bestellen dann die passende Prothese und passen sie an den:die Anwender:in an: „Sie müssen darauf achten“, erklärt Bischof, „dass die Komponenten mit der Pathologie der Verletzung bzw. Erkrankung und der Physiologie der Anwender:innen zusammenpassen.“ Besonders der Prothesenschaft, also die Anbindung an den Körper, ist maßgeschneidert: Länge und Dimensionierung müssen passen.
Ottobock beteiligt sich auch an der Entwicklung von Therapie- und Trainingskonzepten, um Rückschlüsse für die Weiterentwicklung der Komponenten und die optimalen Prozessabläufe ziehen zu können. Daher werden im Firmenverbund Orthopädietechniker:innen sowie Physio- und Ergotherapeut:innen in eigenen Versorgungszentren beschäftigt. Weltweit werden Schulungen zu den neuesten Technologien, Produkten und deren technischen Möglichkeiten abgehalten: „Wir wollen damit die Qualität in der Versorgung erhöhen“, betont Sima.
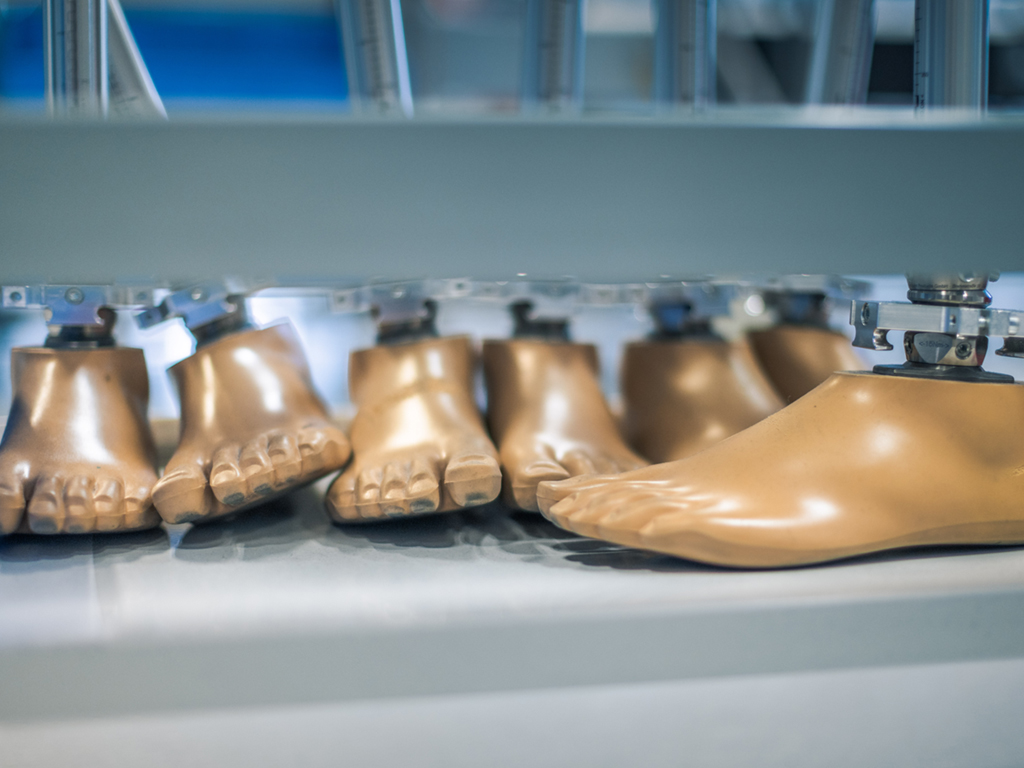
So bedarf es beispielsweise einer Zertifizierung, um ein C-Leg – ein Prothesensystem mit einer sehr ausgefeilten Steuerung, das sich in Echtzeit dem Gangbild der Anwender:innen mit Oberschenkelamputation anpasst – versorgen zu können. Für Sima ist „die ständige Weiterentwicklung Pflicht: Das erste Mikroprozessorknie entstand 1997, aktuell arbeitet Ottobock an der 4. Generation dieser selbstlernenden Systeme.“
Die große Bedeutung maßgeschneiderter Prothetik lässt sich an den Fertigungszahlen ablesen: Allein Ottobock Wien stellt pro Jahr rund 11.000 Einheiten von unteren Extremitäten und 5.000 obere Gliedmaßen her.
Wenn das Kniegelenk mitdenkt
Das in Wien gefertigte Myo-Plus-Mustererkennungssystem ist für Entwicklungsleiter Sima „ein Meilenstein, weil zum ersten Mal die Prothese von den Anwender:innen lernt: Im Vergleich zur konventionellen 2-Kanal-Myo-Signal-Ansteuerung, bei der nur das Öffnen und Schließen ohne Umschaltung gesteuert wird, bietet sich nun eine Vielzahl von intuitiv steuerbaren Griffmöglichkeiten.“ Das System ist selbstlernend und die Anwender:innen können es trainieren: „Auch beim Kniegelenk ermittelt die Steuerung auf Basis der gemessenen Sensordaten die Intention der Anwender:innen und stellt sich auf die aktuelle Gangsituation ein.“
Der KI blind folgen, ohne Wenn und Aber? @martinamara, Professorin für Roboterpsychologie, hält nichts davon. Die KI kann nämlich längst nicht alles. Im Interview verrät Mara, wie wir Künstliche Intelligenz dennoch zu unserem Vorteil nutzen können: https://t.co/UftkfshC40 pic.twitter.com/BIGN3c1FOH
— Arbeit&Wirtschaft Magazin (@AundWMagazin) July 20, 2023
Die Entwicklerin Birgit Bischof erklärt, dass die Steuerprogramme durch die Anwendung der KI verschiedene Abläufe und Bewegungszustände als Muster erkennen können und die gewünschten Prothesenbewegungen ausführen. Im Vergleich zur Hand sei der menschliche Gang in klaren Phasen abgegrenzt. Das System sammelt Daten, in welchem Winkel der Fuß jeweils zum Knie steht. „Daraus kann es dann schließen, wie es sich verhalten soll, und ein zyklisches Gangmuster ableiten: Da denkt das Kniegelenk dann sozusagen mit.“
Elektroden zwischen der Prothese und den Muskeln sammeln diese Daten. Der Muskel erfasst schließlich die elektrischen Steuersignale aus dem Gehirn, der als Signalverstärker dient.
KI zeigt Muskeln
Eine Besonderheit sei die „ganzheitliche Abbildung der Muskelspannung durch acht lokale Elektroden. Dieses Impulsmuster kann die künstliche Intelligenz dann auf die Griffintention der Anwender:innen abbilden“, so Sima. Für jeden Griff gebe es ein Bild, das individuell und einzigartig zuordenbar sei: „Die KI verlinkt das Muster mit der gewünschten Bewegung. Anwender:innen müssen mit dem System üben und es dadurch immer präziser trainieren.“
Die Software nimmt dabei muskuläre Reize auf und ordnet sie einer bestimmten Bewegung zu. Beim nächsten Reiz macht die Prothese dann die Bewegung, die die Software der jeweiligen Muskelspannung zugeordnet hat: „Anwender:innen programmieren sich ihre Griffe mithilfe einer App selbst, die Abläufe werden dadurch automatisiert.“ Für Sima macht „die KI den großen Unterschied. Die Prothese lernt von Anwender:innen und nicht umgekehrt.“
Technisch sieht Sima in der Anwendung der Myo-Technologie noch großes Potenzial: „Wir forschen in Richtung simultaner Steuerung: Mehrere Bewegungen sequenziell hintereinander zu machen empfinden viele als störend, die Herausforderung der Zukunft liegt in der Gleichzeitigkeit.“